Лазерная резка нержавеющей стали – одна из самых востребованных и технологически продвинутых операций в современной металлообработке. Нержавеющая сталь, благодаря своим уникальным свойствам – коррозионной стойкости, прочности и эстетичному внешнему виду – находит применение в самых разнообразных отраслях, от пищевой промышленности и медицины до машиностроения и дизайна. Резка нержавейки лазером позволяет получать изделия сложной конфигурации с высокой точностью и качеством кромки.
Однако, несмотря на кажущуюся простоту, обработка нержавеющей стали лазером имеет свои специфические особенности и нюансы. Этот материал требует особого подхода из-за своих физико-химических свойств, таких как высокая отражающая способность и низкая теплопроводность. Неправильный выбор технологии или параметров резки может привести к дефектам, снижению коррозионной стойкости и увеличению затрат.
Цель этой статьи – подробно рассмотреть особенности лазерной резки нержавеющей стали, ключевые нюансы технологии, влияющие на качество конечного продукта, и дать практические рекомендации. Мы разберем, какой газ лучше использовать, какие типы лазеров подходят для нержавеющей стали и ее лазерной резки, как правильно настроить параметры, а также какие проблемы могут возникнуть и как их эффективно решать. Это руководство будет полезно как заказчикам услуг лазерной резки нержавейки, так и специалистам, стремящимся углубить свои знания в этой области.
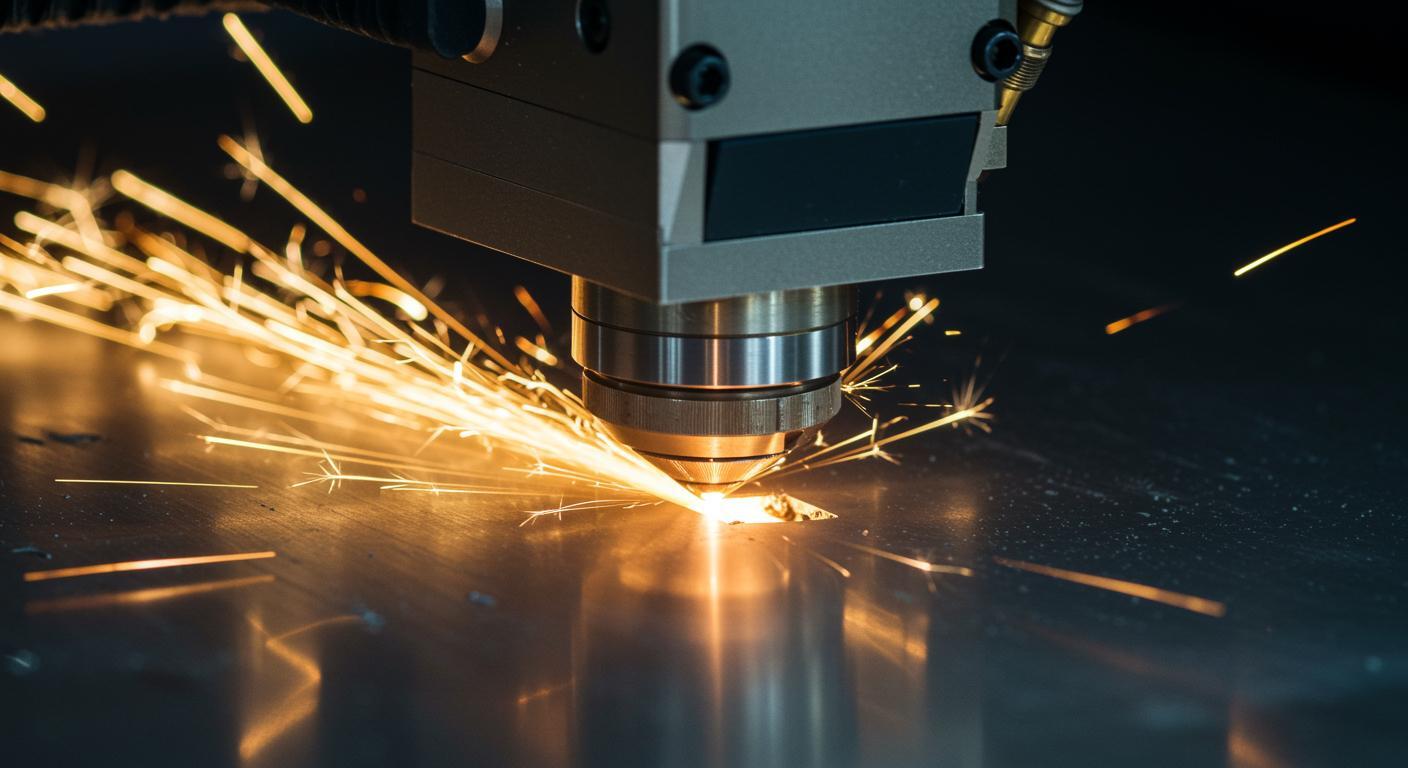
Почему выбирают лазерный раскрой нержавейки: Ключевые достоинства технологии
Лазерный раскрой нержавейки завоевал популярность благодаря ряду неоспоримых преимуществ перед традиционными методами механической резки (например, плазменной, гидроабразивной или штамповкой). Эти достоинства делают его предпочтительным выбором для множества применений.
Высокая точность и качество реза
Лазерный луч можно сфокусировать до очень малого диаметра (десятые доли миллиметра), что обеспечивает минимальную ширину реза (керф). Это позволяет изготавливать детали с высокой точностью (до ±0.1 мм и даже точнее, в зависимости от оборудования и толщины материала). При правильном подборе параметров и использовании инертных газов (например, азота), кромка реза получается гладкой, чистой, без заусенцев и окалины, что часто исключает необходимость в последующей механической обработке.
Минимальная зона термического влияния (ЗТВ)
Благодаря высокой концентрации энергии в малой точке и высокой скорости процесса, зона термического влияния (ЗТВ) при лазерной резке нержавейки очень мала. Это означает, что структура и свойства материала вблизи реза изменяются незначительно. Минимальная ЗТВ особенно важна для нержавеющей стали, так как перегрев может привести к выгоранию легирующих элементов (например, хрома), снижению коррозионной стойкости и изменению механических свойств.
Возможность изготовления сложных контуров и мелких деталей
Лазерные станки управляются ЧПУ (числовым программным управлением), что позволяет вырезать детали практически любой сложности, включая острые углы, мелкие отверстия, сложные криволинейные контуры и ажурные узоры. Это открывает широкие возможности для дизайнеров и инженеров при создании уникальных изделий из нержавеющей стали.
Высокая скорость обработки (особенно для тонколистовой нержавейки)
Для тонколистовой нержавеющей стали (обычно до 5-6 мм) лазерная резка нержавейки обеспечивает очень высокую скорость процесса, значительно превосходящую многие другие методы. Это ведет к повышению производительности и снижению стоимости изготовления деталей.
Бесконтактный метод резки: Отсутствие механического воздействия на материал
Лазерный луч режет материал, не касаясь его физически. Это исключает механические деформации, особенно важные при работе с тонкими листами нержавейки, а также износ режущего инструмента, характерный для контактных методов.
Экономичность при малых и средних партиях, гибкость производства
Лазерная резка нержавеющей стали не требует изготовления дорогостоящей оснастки (штампов, пресс-форм), что делает ее экономически выгодной даже для единичных изделий и небольших партий. Перенастройка станка на изготовление другой детали занимает минимум времени – достаточно загрузить новый файл чертежа в систему ЧПУ. Это обеспечивает высокую гибкость производства.
Особенности нержавеющей стали как материала для лазерной обработки
Нержавеющая сталь – это сложный легированный сплав, чьи уникальные свойства не только обеспечивают ее превосходные эксплуатационные характеристики, но и накладывают определенные особенности на процесс лазерной резки. Понимание этих нюансов критически важно для получения качественного результата при резке нержавеющей стали лазером.
Высокая отражающая способность
Нержавеющая сталь, особенно полированная или зеркальная, обладает высокой отражающей способностью для лазерного излучения, особенно в инфракрасном диапазоне, характерном для CO2-лазеров. Это означает, что часть энергии лазера отражается от поверхности, а не поглощается материалом, что может снизить эффективность резки. Оптоволоконные лазеры, имеющие меньшую длину волны, лучше поглощаются нержавеющей сталью, что делает их более предпочтительными для этой задачи. Для CO2-лазеров иногда применяют специальные покрытия или изменяют угол падения луча для улучшения поглощения.
Низкая теплопроводность (по сравнению с углеродистой сталью)
Нержавеющая сталь имеет значительно более низкую теплопроводность по сравнению с углеродистыми сталями. Это приводит к тому, что тепло, генерируемое лазерным лучом, концентрируется в зоне реза и медленнее отводится вглубь материала. С одной стороны, это способствует более эффективному плавлению. С другой стороны, это может привести к локальному перегреву, увеличению зоны термического влияния (если параметры подобраны неверно), и, как следствие, к деформации тонких деталей или выгоранию легирующих элементов.
Высокое содержание хрома
Основным легирующим элементом нержавеющей стали является хром (Cr), который обеспечивает ее коррозионную стойкость за счет образования на поверхности тонкой защитной оксидной пленки (пассивного слоя). При лазерной резке нержавейки с использованием кислорода в качестве вспомогательного газа, хром активно окисляется, образуя тугоплавкие оксиды (например, Cr2O3). Эти оксиды могут формировать на кромке реза твердую, шероховатую окалину темного цвета, которую сложно удалить. Кроме того, окисление хрома снижает коррозионную стойкость материала в зоне реза. Поэтому для получения "чистого реза" без окалины чаще всего используют инертные газы, такие как азот.
Различные марки нержавеющей стали
Существует множество марок нержавеющей стали, различающихся по химическому составу и структуре (аустенитные, ферритные, мартенситные, дуплексные). Наиболее распространены аустенитные стали типа AISI 304 (08Х18Н10) и AISI 316 (08Х17Н13М2). Разные марки могут иметь несколько отличающиеся теплофизические свойства и по-разному вести себя при обработке нержавеющей стали лазером. Например, стали с более высоким содержанием легирующих элементов могут требовать коррекции параметров резки.
Наличие защитной пленки на некоторых видах нержавейки
Многие виды листовой нержавеющей стали, особенно с декоративной поверхностью (шлифованная, зеркальная), поставляются с защитной полимерной пленкой. Резка нержавейки вместе с пленкой возможна и часто практикуется для защиты поверхности от царапин и брызг расплавленного металла. Однако наличие пленки вносит свои нюансы:
- Продукты горения пленки могут загрязнять оптику лазера.
- Необходимо подбирать параметры так, чтобы пленка испарялась или сгорала без образования нагара на кромке.
- Для некоторых типов пленок может потребоваться использование азота для предотвращения оплавления краев пленки.
Понимание этих особенностей нержавеющей стали позволяет технологам правильно выбирать оборудование, вспомогательные газы и режимы лазерной резки нержавейки для достижения оптимального качества и производительности.
Выбор оборудования и технологии для эффективной резки нержавейки лазером
Эффективность и качество лазерной резки нержавейки во многом определяются правильным выбором оборудования и применяемой технологии. Современный рынок предлагает различные типы лазерных станков, каждый из которых имеет свои преимущества и ограничения при работе с таким специфическим материалом, как нержавеющая сталь.
Типы лазеров: Оптоволоконные (Fiber) vs. Газовые (CO2) лазеры
Основными типами лазеров, используемых для промышленной резки металлов, включая нержавеющую сталь, являются оптоволоконные (твердотельные) и газовые (CO2) лазеры.
- Преимущества оптоволоконных лазеров для резки нержавейки:
- Лучшее поглощение излучения: Длина волны излучения оптоволоконного лазера (обычно около 1.06-1.08 мкм) значительно лучше поглощается нержавеющей сталью по сравнению с излучением CO2-лазера (10.6 мкм). Это приводит к более эффективному использованию энергии и возможности резки с меньшей мощностью.
- Высокая скорость на тонких и средних толщинах: Оптоволоконные лазеры демонстрируют значительно более высокую скорость резки нержавеющей стали толщиной до 5-6 мм, а иногда и до 10-12 мм, по сравнению с CO2-лазерами аналогичной мощности.
- Меньшие эксплуатационные расходы: Они не требуют использования специальных газов для генерации лазерного луча (как гелий, азот и CO2 в CO2-лазерах), имеют более высокий КПД (до 30-35% против 10-15% у CO2) и меньшие затраты на техническое обслуживание (отсутствие зеркал в резонаторе, требующих юстировки и чистки).
- Возможность резки высокоотражающих материалов: Лучше справляются с резкой полированной нержавейки.
- Возможности и ограничения CO2-лазеров при обработке нержавеющей стали лазером:
- Качество реза на больших толщинах: Традиционно считалось, что CO2-лазеры обеспечивают несколько лучшее качество кромки (меньшую шероховатость) при резке нержавеющей стали больших толщин (свыше 15-20 мм), однако современные мощные оптоволоконные лазеры практически сравнялись с ними по этому показателю.
- Более высокая стоимость эксплуатации: Требуют регулярной замены газовой смеси, обслуживания зеркал и турбины.
- Меньшая эффективность при резке тонколистовой нержавейки.
В целом, для лазерной резки нержавеющей стали, особенно тонколистовой и средней толщины, оптоволоконные лазеры сегодня являются более предпочтительным и экономически выгодным выбором.
Ключевые компоненты лазерного станка, важные для качества резки нержавейки
Помимо типа самого лазерного источника, на качество резки нержавейки лазером влияют и другие компоненты станка:
- Режущая голова: Это узел, который фокусирует лазерный луч на поверхность материала и подает вспомогательный газ в зону реза. Качество оптики (фокусирующей линзы), точность системы фокусировки и конструкция сопла играют ключевую роль. Для нержавейки важно использовать сопла, обеспечивающие ламинарный поток газа и эффективное удаление расплава.
- Система подачи вспомогательного газа: Должна обеспечивать стабильную подачу газа (азота, кислорода или воздуха) под необходимым давлением и с высокой степенью чистоты, особенно при работе с азотом для получения "чистого реза".
- Система ЧПУ и программное обеспечение: Современные системы ЧПУ обеспечивают высокую точность позиционирования и плавность движения режущей головы. Специализированное ПО позволяет оптимизировать траекторию резки, управлять параметрами лазера и газа, а также использовать функции для улучшения качества на углах и мелких элементах (например, контроль мощности, изменение скорости).
- Станина и портал станка: Жесткость и виброустойчивость конструкции станка важны для поддержания точности на высоких скоростях резки.
Выбор современного, правильно сконфигурированного лазерного комплекса является основой для предоставления качественных услуг лазерной резки нержавейки.
Выбор вспомогательного газа – залог качества при лазерной резке нержавейки
Одним из самых критических нюансов лазерной резки нержавеющей стали является правильный выбор вспомогательного (режущего) газа. Газ выполняет несколько функций: защищает зону реза от воздействия окружающего воздуха, удаляет расплавленный металл из зоны реза и, в некоторых случаях, участвует в экзотермической реакции, увеличивая эффективность процесса. Для резки нержавейки лазером в основном используют азот, кислород или сжатый воздух.
Лазерная резка нержавейки азотом (N2) – для "чистого реза"
Резка нержавеющей стали с использованием азота высокой чистоты (обычно 99.995% и выше) называется "резкой плавлением" или "чистым резом" (clean cut, bright cut).
- Механизм действия: Азот является инертным газом по отношению к нержавеющей стали при температурах резки. Его основная функция – механическое выдувание расплавленного лазером металла из зоны реза под высоким давлением (до 15-22 бар и выше). При этом азот предотвращает окисление хрома и железа, защищая кромки реза.
- Преимущества:Блестящая, светлая кромка без окалины: Поверхность реза остается металлической, без оксидной пленки.
- Сохранение коррозионной стойкости: Отсутствие окисления означает, что пассивный слой нержавеющей стали не нарушается так сильно, как при резке кислородом.
- Идеально для последующей сварки: Кромки, полученные резкой в азоте, можно сваривать без дополнительной механической зачистки.
- Подходит для пищевой и медицинской промышленности: Где требования к чистоте поверхности особенно высоки.
- Недостатки:Более высокое давление и расход газа: Требует значительных объемов азота высокой чистоты, что увеличивает стоимость процесса.
- Несколько ниже скорость резки по сравнению с кислородом на больших толщинах: Энергия лазера тратится только на плавление, без дополнительного тепла от экзотермической реакции.
Лазерная резка нержавейки кислородом (O2) – для увеличения скорости на определенных толщинах
Резка нержавеющей стали с использованием кислорода называется "кислородной резкой" или "резкой горения".
- Механизм действия: Кислород вступает в экзотермическую реакцию с расплавленным металлом (в основном с железом), выделяя дополнительное тепло. Это тепло помогает процессу резки, позволяя увеличить скорость или прорезать большие толщины при той же мощности лазера. Расплавленные оксиды выдуваются из зоны реза потоком кислорода, подаваемого под относительно низким давлением (обычно до 6 бар).
- Преимущества:Более высокая скорость резки толстой нержавейки (обычно свыше 3-4 мм).
- Меньший расход газа и более низкое давление по сравнению с азотом.
- Недостатки:Образование оксидной пленки на кромке: Кромка реза получается темной, матовой и покрытой слоем оксидов (в основном оксиды железа и хрома).
- Необходимость последующей обработки кромки: Оксидную пленку часто требуется удалять механически (шлифовка, зачистка) или химически (травление), если требуется чистая поверхность для сварки, покраски или по эстетическим соображениям.
- Снижение коррозионной стойкости: Оксидный слой может быть менее стойким к коррозии, чем основной металл.
- Больше грата (дросса): Часто образуется больше заусенцев на нижней кромке.
Использование сжатого воздуха – экономичный, но компромиссный вариант
Резка с использованием очищенного и осушенного сжатого воздуха также возможна.
- Состав воздуха: Воздух состоит примерно из 78% азота и 21% кислорода.
- Результат: Качество реза является промежуточным между резкой чистым азотом и чистым кислородом. На кромке образуется тонкая оксидная пленка, но обычно менее выраженная, чем при резке чистым кислородом. Цвет кромки может варьироваться от светло-желтого до коричневатого.
- Преимущества: Значительно дешевле, чем использование баллонного азота или кислорода, так как воздух генерируется компрессором.
- Недостатки: Качество реза ниже, чем при использовании азота. Не подходит для применений, где требуется идеальная чистота кромки или максимальная коррозионная стойкость. Есть ограничения по толщине эффективно разрезаемой нержавейки. Важна качественная подготовка воздуха (осушение, фильтрация от масла и твердых частиц).
Давление и чистота газа: Важные параметры для стабильного процесса
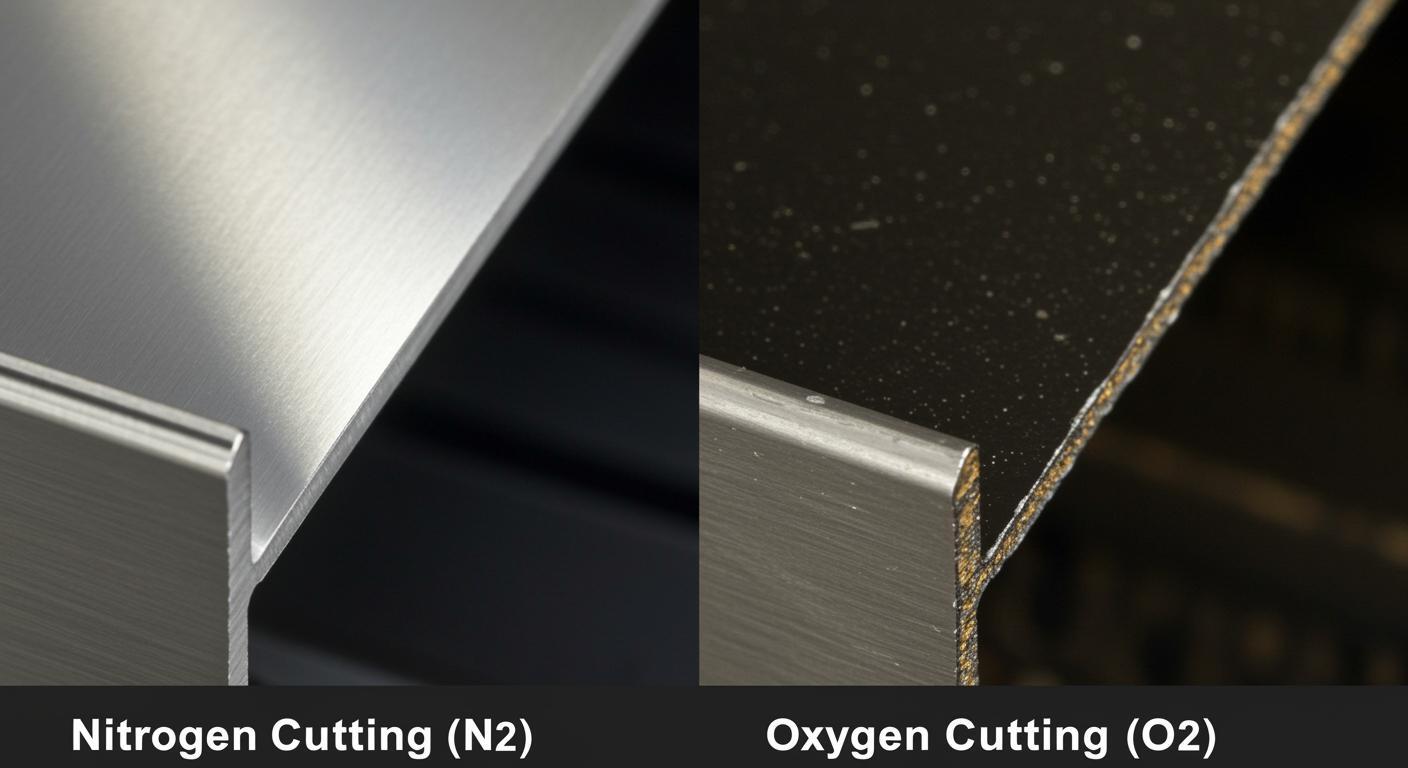
Независимо от выбранного газа, его давление и чистота играют важную роль.
- Давление газа: Должно быть достаточным для эффективного удаления расплава. Слишком низкое давление приведет к образованию грата, слишком высокое (особенно для кислорода) может вызвать неконтролируемое горение или охлаждение зоны реза.
- Чистота газа: Особенно критична для азота. Примеси кислорода или влаги в азоте могут привести к легкому окислению и потемнению кромки, снижая качество "чистого реза".
Выбор вспомогательного газа для лазерной резки нержавеющей стали зависит от требований к качеству кромки, толщины материала, последующих операций и экономических соображений. Для большинства высококачественных применений нержавейки предпочтение отдается резке азотом.
Настройка параметров – путь к оптимальной резке нержавейки лазером
Достижение высокого качества при лазерной резке нержавейки невозможно без точной настройки рабочих параметров лазерного станка. Эти параметры взаимосвязаны и должны подбираться с учетом толщины и марки нержавеющей стали, типа используемого лазера и вспомогательного газа.
Мощность лазерного излучения
Мощность лазера – один из ключевых параметров, определяющих возможность резки материала определенной толщины.
- Подбор: Чем толще нержавеющая сталь, тем большая мощность лазера требуется для ее эффективного проплавления. Однако избыточная мощность при резке тонких листов может привести к перегреву, увеличению ширины реза и деформации. Современные станки позволяют точно регулировать мощность.
- Влияние: Недостаточная мощность приведет к неполному прорезанию или образованию большого количества грата.
Скорость резки
Скорость резки – это скорость перемещения режущей головы вдоль контура детали.
- Взаимосвязь: Скорость напрямую связана с мощностью лазера и толщиной материала. При увеличении мощности можно увеличить скорость резки, и наоборот. Для более толстых материалов скорость резки снижается.
- Влияние на качество: Слишком высокая скорость может привести к неполному прорезанию, обрыву реза или ухудшению качества кромки (появлению "волн"). Слишком низкая скорость может вызвать перегрев, оплавление кромок, увеличение ширины реза и образование грата, особенно на тонких листах.
Фокусное расстояние и положение фокуса
Лазерный луч фокусируется линзой в режущей голове в пятно малого диаметра.
- Фокусное расстояние линзы: Определяет глубину фокуса и размер пятна. Для резки нержавейки разной толщины могут использоваться линзы с разным фокусным расстоянием.
- Положение фокуса: Точка фокуса может быть расположена на поверхности материала, над поверхностью или под поверхностью. Оптимальное положение фокуса зависит от толщины материала, типа газа и требуемого качества кромки. Например, при резке тонкой нержавейки азотом фокус часто устанавливают на поверхность или немного ниже, а при резке толстой нержавейки кислородом – немного выше поверхности. Неправильное положение фокуса приводит к увеличению ширины реза, ухудшению качества кромки и образованию грата.
Диаметр сопла и расстояние от сопла до материала
Сопло в режущей голове направляет поток вспомогательного газа в зону реза.
- Диаметр сопла: Подбирается в зависимости от толщины материала и типа газа. Меньшие диаметры сопел используются для тонких материалов и резки азотом под высоким давлением, большие – для толстых материалов и резки кислородом.
- Расстояние от сопла до материала (зазор): Обычно составляет 0.5-2 мм. Этот параметр влияет на эффективность удаления расплава и стабильность потока газа. Неправильный зазор может привести к образованию грата или загрязнению сопла.
Частота и скважность импульсов (для импульсных лазеров)
Хотя большинство современных систем для резки металлов работают в непрерывном режиме (CW - Continuous Wave), некоторые задачи (например, резка очень тонких материалов или перфорация) могут выполняться в импульсном режиме.
- Частота импульсов: Количество импульсов в секунду.
- Скважность (рабочий цикл): Отношение длительности импульса к периоду их следования.
- Эти параметры влияют на тепловложение и позволяют более точно контролировать процесс для деликатных операций.
Примеры рекомендуемых режимов для разных толщин нержавейки
Точные параметры лазерной резки нержавейки являются ноу-хау многих производителей и операторов оборудования, так как они зависят от конкретной модели станка, его состояния и даже от партии материала. Однако, в качестве общего ориентира можно привести примеры (значения могут сильно варьироваться):
- Нержавеющая сталь 1 мм (резка азотом, оптоволоконный лазер 2 кВт):Скорость: 15-25 м/мин
- Давление азота: 16-20 бар
- Положение фокуса: 0 / -0.5 мм от поверхности
- Нержавеющая сталь 5 мм (резка азотом, оптоволоконный лазер 4 кВт):Скорость: 2.5-4 м/мин
- Давление азота: 18-22 бар
- Положение фокуса: -1.0 / -2.0 мм от поверхности
- Нержавеющая сталь 10 мм (резка кислородом, оптоволоконный лазер 6 кВт):Скорость: 1.0-1.8 м/мин
- Давление кислорода: 0.5-0.8 бар
- Положение фокуса: +1.0 / +2.0 мм от поверхности
Операторы лазерных станков обычно используют библиотеки режимов, предоставленные производителем оборудования, и корректируют их на основе практического опыта для достижения наилучшего качества резки нержавеющей стали лазером.
Типичные проблемы и дефекты при резке нержавеющей стали лазером и их решения
Несмотря на высокую точность и технологичность лазерной резки нержавейки, при неправильной настройке параметров или из-за особенностей материала могут возникать различные проблемы и дефекты. Знание этих потенциальных проблем и способов их устранения важно для получения качественных изделий.
Образование грата (дросса, заусенцев) на нижней кромке реза
Грат – это застывшие капли расплавленного металла, прилипшие к нижней кромке реза. Это один из самых частых дефектов.
- Причины:Недостаточное давление или неправильный тип вспомогательного газа (неэффективное удаление расплава).
- Слишком низкая или слишком высокая скорость резки.
- Неправильное положение фокуса.
- Загрязненное или поврежденное сопло.
- Низкое качество самого материала (например, высокое содержание примесей).
- Методы устранения:Отрегулировать давление и расход газа.
- Оптимизировать скорость резки и положение фокуса.
- Проверить и при необходимости заменить сопло.
- Использовать более качественный материал.
- Для резки азотом – убедиться в его высокой чистоте.
Окалина и изменение цвета кромки (потемнение)
При резке нержавейки кислородом образование темной оксидной пленки (окалины) является нормальным явлением. Однако потемнение кромки может наблюдаться и при резке азотом, если процесс настроен неверно.
- Причины (при резке азотом):Недостаточная чистота азота (примеси кислорода или влаги).
- Низкое давление азота, не обеспечивающее полную защиту зоны реза.
- Перегрев материала из-за слишком низкой скорости резки или высокой мощности.
- Методы устранения (для азотной резки):Использовать азот высокой чистоты (99.995% и выше).
- Увеличить давление азота.
- Оптимизировать скорость резки и мощность лазера.
Непрорезание материала или неровный рез
Иногда лазер не прорезает материал насквозь по всему контуру или оставляет неровную, "рваную" кромку.
- Причины:Недостаточная мощность лазера для данной толщины.
- Слишком высокая скорость резки.
- Неправильное положение фокуса.
- Загрязнение или повреждение оптики (линзы, защитного стекла).
- Проблемы с подачей вспомогательного газа.
- Методы устранения:Увеличить мощность или снизить скорость.
- Скорректировать положение фокуса.
- Проверить и очистить/заменить оптические элементы.
- Проверить систему подачи газа.
Тепловая деформация тонколистовой нержавейки
Из-за низкой теплопроводности нержавеющей стали тонкие листы (менее 1-1.5 мм) могут деформироваться (коробиться) от нагрева в процессе резки, особенно при вырезании длинных контуров или большого количества мелких деталей.
- Методы минимизации:Использовать оптимальные параметры резки (не занижать скорость, не завышать мощность без необходимости).
- Применять специальные режимы резки для тонких листов (например, импульсный режим, если доступен).
- Правильно располагать детали на листе (нестинг), оставляя достаточные перемычки или используя специальные стратегии врезки и обхода контура.
- Обеспечить надежное крепление листа на столе станка.
- Использовать охлаждение (например, обдув воздухом), если это возможно.
Микротрещины и оплавление острых углов
На острых углах или очень мелких элементах может происходить избыточное тепловложение, приводящее к оплавлению или образованию микротрещин.
- Методы устранения:Использование функций ЧПУ для снижения скорости и мощности на углах (corner control).
- Скругление очень острых внутренних углов небольшим радиусом (если это допустимо по чертежу).
- Оптимизация параметров резки.
Успешное решение этих проблем требует опыта оператора и хорошего понимания взаимодействия лазерного излучения с нержавеющей сталью. Регулярное техническое обслуживание оборудования также играет важную роль в предотвращении многих дефектов резки нержавеющей стали лазером.
Финишные операции и контроль качества изделий из нержавейки после лазерной резки
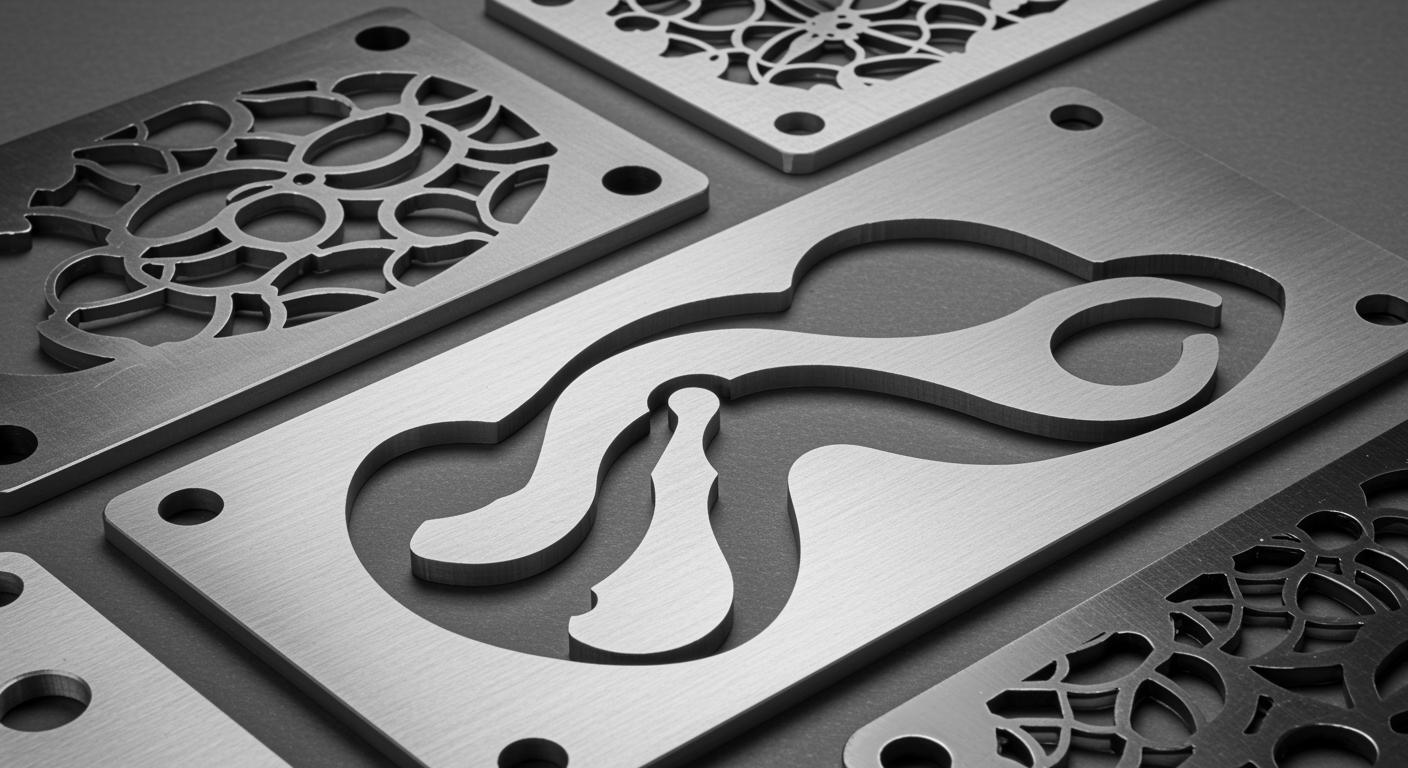
Даже при идеально настроенном процессе лазерной резки нержавейки, для получения готового изделия часто требуются некоторые финишные операции и обязательный контроль качества. Объем этих операций зависит от исходных требований к детали и от того, какой вспомогательный газ использовался при резке.
Необходимость удаления защитной пленки (если использовалась)
Если резка нержавеющей стали лазером производилась с защитной полимерной пленкой, ее необходимо аккуратно удалить с готовых деталей. Иногда края пленки могут слегка оплавиться и потребовать более тщательного удаления.
Удаление грата и зачистка кромок
- При резке азотом ("чистый рез"): Обычно грат минимален или отсутствует. Если небольшие заусенцы все же есть, их можно легко удалить ручным инструментом или легкой шлифовкой.
- При резке кислородом: Образуется оксидная пленка и, как правило, больше грата. Удаление оксидной пленки и грата является обязательным, если требуется чистая металлическая поверхность для сварки, покраски, или если деталь имеет эстетическое назначение. Это может производиться:
- Механически: шлифовальными машинами, щетками, галтовкой (для мелких деталей).
- Химически: травлением в специальных растворах (требует осторожности и соблюдения техники безопасности).
Восстановление пассивного слоя (пассивация) для критически важных применений
При любом виде термической резки, включая лазерную, а также при последующей механической обработке, пассивный слой нержавеющей стали, обеспечивающий ее коррозионную стойкость, может быть нарушен или загрязнен частицами железа от инструмента. Для ответственных деталей, эксплуатируемых в агрессивных средах (например, в пищевой, химической, медицинской промышленности), может потребоваться операция пассивации. Пассивация – это химический процесс обработки поверхности нержавеющей стали (обычно растворами азотной или лимонной кислоты), который удаляет загрязнения и способствует восстановлению и утолщению защитного оксидного слоя хрома.
Методы контроля качества реза
Контроль качества вырезанных деталей включает:
- Визуальный осмотр: Проверка на наличие грата, окалины, непрорезов, оплавления кромок, соответствия чистоты поверхности требованиям.
- Инструментальный контроль:Проверка геометрических размеров и допусков с помощью штангенциркулей, микрометров, шаблонов, измерительных проекторов или координатно-измерительных машин (КИМ).
- Контроль шероховатости кромки (при необходимости) с помощью профилометров.
- Проверка перпендикулярности реза.
Тщательный контроль на всех этапах, начиная от проверки входного материала и заканчивая приемкой готовых деталей, обеспечивает высокое качество изделий, полученных методом лазерной резки нержавеющей стали.
Как выбрать надежного поставщика услуг лазерной резки нержавейки
Выбор подрядчика для выполнения услуг лазерной резки нержавейки – ответственный шаг, от которого зависит качество, сроки и стоимость ваших изделий. Учитывая особенности и нюансы работы с этим материалом, стоит обратить внимание на несколько ключевых аспектов.
Опыт работы именно с нержавеющей сталью
Нержавеющая сталь требует специфических знаний и навыков. Уточните, имеет ли компания достаточный опыт лазерной резки нержавейки различных марок и толщин. Попросите показать примеры выполненных работ именно из нержавеющей стали.
Наличие современного оборудования (предпочтительно оптоволоконные лазеры)
Современные оптоволоконные лазерные комплексы обеспечивают более высокую скорость, точность и качество реза нержавеющей стали, особенно тонколистовой, по сравнению со старыми CO2-лазерами. Узнайте о парке оборудования исполнителя: тип лазеров, их мощность, год выпуска, производитель. Наличие систем автоматической смены паллет, загрузки/выгрузки листа также говорит о серьезном подходе к производству.
Возможность использования различных вспомогательных газов (особенно азота высокой чистоты)
Для получения "чистого реза" без окалины, что часто является критичным для нержавейки, необходимо использовать азот высокой чистоты (99.995% и выше) под высоким давлением. Убедитесь, что у исполнителя есть возможность резки азотом, а также кислородом и сжатым воздухом для различных задач и толщин. Наличие собственной азотной станции или надежных поставщиков чистого газа – хороший знак.
Примеры работ, отзывы клиентов
Попросите портфолио выполненных заказов, особенно из нержавеющей стали. Поищите отзывы о компании от других клиентов. Репутация на рынке и рекомендации могут многое сказать о надежности подрядчика.
Готовность обсуждать технические нюансы и предоставлять консультации
Компетентный исполнитель всегда готов обсудить технические детали вашего заказа, дать рекомендации по оптимизации чертежей для лазерного раскроя нержавейки, выбору материала или типа реза. Если представители компании уклоняются от технических вопросов или не могут внятно объяснить технологические аспекты, это повод задуматься.
Контроль качества и сертификация
Узнайте, какая система контроля качества внедрена на производстве. Наличие сертификатов (например, ISO 9001) может свидетельствовать о высоком уровне организации производственных процессов.
Сроки выполнения и ценовая политика
Сравните предложения от нескольких компаний по срокам и стоимости. Однако не стоит гнаться за самой низкой ценой в ущерб качеству, особенно когда речь идет о таком требовательном материале, как нержавеющая сталь. Слишком низкая цена может означать использование устаревшего оборудования, некачественных газов или недостаточный контроль качества.
Тщательный подход к выбору исполнителя услуг лазерной резки нержавейки поможет вам избежать проблем и получить изделия, полностью соответствующие вашим ожиданиям.