В современной промышленности, где точность, скорость и экономичность играют решающую роль, выбор лазера для резки металла становится стратегически важной задачей. На рынке доминируют два основных типа лазерных технологий: традиционный CO2 лазер для металла и более современный волоконный (оптоволоконный) лазер для металла. Каждый из них обладает своими уникальными характеристиками, преимуществами и ограничениями. Эта статья предлагает детальное сравнение CO2 и волоконных лазеров, анализируя их производительность, экономику и области применения, чтобы помочь вам определить, какой лазер лучше для резки металла в ваших конкретных производственных условиях и ответить на главный вопрос: CO2 или волоконный лазер?
Принципы работы и ключевые характеристики лазеров
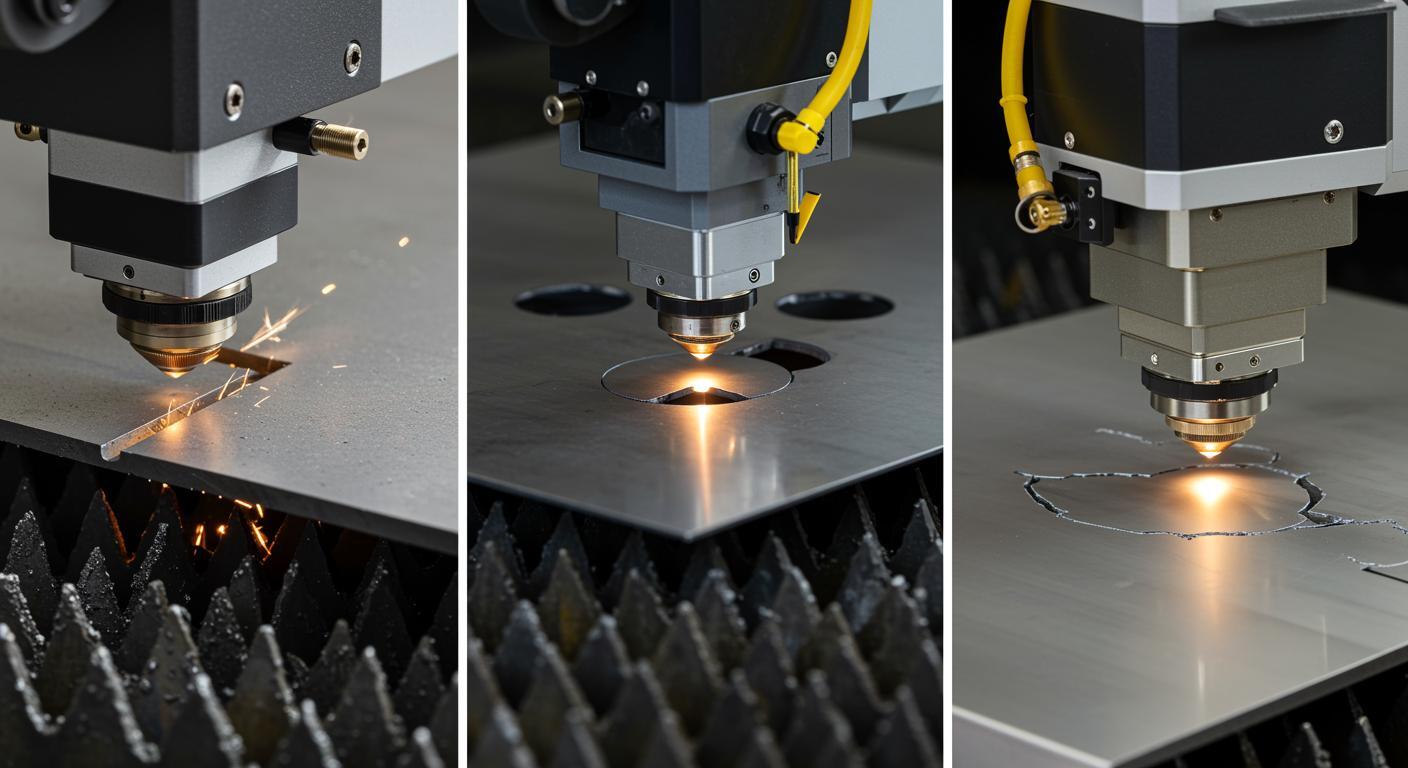
Понимание фундаментальных различий в принципах генерации и доставки лазерного излучения является первым шагом к осознанному выбору.
CO2 лазер для резки металла
CO2 лазеры – это газовые лазеры, в которых активной средой служит смесь газов, состоящая преимущественно из углекислого газа (CO2), азота (N2) и гелия (He). Электрический разряд возбуждает молекулы азота, которые затем передают энергию молекулам CO2, вызывая генерацию лазерного излучения.
- Длина волны: Стандартная длина волны для CO2-лазера составляет 10.6 микрометра (мкм). Эта относительно длинная волна хорошо поглощается многими неметаллическими материалами, но хуже – металлами, особенно цветными и с высокой отражающей способностью.
- Система доставки луча: Излучение от резонатора к режущей головке передается с помощью системы зеркал. Эта система требует точной юстировки и регулярного обслуживания (чистки, замены зеркал), так как загрязнение или смещение зеркал приводит к потере мощности и ухудшению качества луча.
- Применение: CO2-лазеры десятилетиями успешно применяются для лазерной резки металла CO2, особенно углеродистых сталей, а также для резки широкого спектра неметаллов (дерево, пластик, акрил, ткань, кожа).
Волоконный (оптоволоконный) лазер для резки металла
Волоконные лазеры относятся к твердотельным лазерам. Активной средой в них служит оптическое волокно, легированное редкоземельными элементами, чаще всего иттербием. Накачка активного волокна осуществляется полупроводниковыми лазерными диодами.
- Длина волны: Волоконные лазеры генерируют излучение с длиной волны около 1.06-1.08 мкм. Эта длина волны примерно в 10 раз короче, чем у CO2-лазера, и значительно лучше поглощается металлами, включая высокоотражающие, такие как медь, латунь и алюминий.
- Система доставки луча: Лазерный луч передается от источника к режущей головке по гибкому транспортному оптоволокну. Такая система не требует юстировки, более надежна, компактна и менее подвержена влиянию вибраций и загрязнений.
- Применение: Лазерная резка металла волоконным лазером стремительно завоевала рынок благодаря высокой эффективности при работе с металлами, особенно тонколистовыми и среднелистовыми. Оптоволоконный лазер резка металла – это синоним высокой скорости и низких эксплуатационных затрат для многих задач.
Волоконный лазер против CO2: Детальный анализ производительности и экономики
Рассмотрим ключевые параметры, по которым происходит сравнение CO2 и волоконных лазеров.
Эффективность преобразования энергии (КПД) и энергопотребление
- Волоконные лазеры: Обладают значительно более высоким КПД (эффективностью преобразования электрической энергии в световую) – обычно 30-50% и выше.
- CO2 лазеры: Имеют КПД в диапазоне 7-15%.
- Это означает, что волоконный лазер для металла потребляет в 2-5 раз меньше электроэнергии для генерации той же оптической мощности, что и CO2 лазер для металла. Это напрямую сказывается на снижении эксплуатационных расходов.
Скорость резки различных металлов и толщин
- Лазерная резка металла волоконным лазером: Демонстрирует значительно более высокие скорости резки тонколистовых металлов (до 5-6 мм, а иногда и до 10-12 мм), особенно нержавеющей стали и алюминия. Преимущество может быть двукратным и более.
- Лазерная резка металла CO2: Исторически CO2-лазеры имели преимущество при резке углеродистой стали больших толщин (свыше 20-25 мм) с использованием кислорода в качестве вспомогательного газа, обеспечивая хорошее качество кромки. Однако современные мощные волоконные лазеры (12 кВт и выше) активно догоняют и даже превосходят CO2-лазеры и в этом сегменте.
- Для тонких металлов (до 3-4 мм) волоконный лазер против CO2 выигрывает по скорости в разы.
Качество реза и обработка кромок
- CO2 лазеры: При резке толстых углеродистых сталей кислородом могут обеспечивать очень гладкую кромку. При резке нержавеющей стали азотом качество кромки также высокое.
- Волоконные лазеры: Изначально уступали CO2 по качеству реза на некоторых толщинах нержавеющей стали, но современные мощные источники и оптимизированные режущие головки позволяют достигать сопоставимого или даже лучшего качества. На тонких материалах обеспечивают минимальную шероховатость и отсутствие грата.
- Зона термического влияния (ЗТВ) у волоконных лазеров обычно меньше из-за более высокой скорости и лучшей фокусировки.
Обрабатываемые материалы
- Углеродистая сталь: Оба типа лазеров хорошо справляются с этим материалом.
- Нержавеющая сталь: Оба типа эффективны, но волоконные лазеры обычно быстрее на тонких и средних толщинах.
- Алюминий, медь, латунь (цветные/отражающие металлы): Здесь явное преимущество у волоконных лазеров. Их длина волны значительно лучше поглощается этими материалами, что позволяет резать их стабильно и с высоким качеством. CO2 лазеры для металла испытывают серьезные трудности с резкой таких материалов из-за высокого отражения излучения, что может привести к повреждению оптики станка.
- Неметаллы: CO2-лазеры значительно лучше подходят для резки органических материалов (дерево, пластик, акрил, кожа, ткань), так как их длина волны хорошо поглощается этими материалами. Волоконные лазеры для этих задач практически не применяются.
Максимальные и оптимальные толщины резки
- Волоконные лазеры: Оптимальны для резки металлов толщиной до 20-25 мм, хотя современные сверхмощные системы (20-40 кВт и выше) способны резать сталь толщиной 50 мм и более.
- CO2 лазеры: Традиционно использовались для резки углеродистой стали до 25-30 мм, а иногда и толще. Однако их эффективность на таких толщинах часто ниже, чем у современных мощных волоконных аналогов.
Эксплуатационные расходы
- Волоконные лазеры:Значительно ниже энергопотребление.
- Отсутствие необходимости в лазерных газах для резонатора (как у CO2).
- Более длительный срок службы диодов накачки (обычно 50 000 – 100 000 часов).
- Меньше расходных материалов для системы доставки луча (нет зеркал).
- CO2 лазеры:Высокое энергопотребление.
- Необходимость регулярной замены или регенерации газовой смеси в резонаторе.
- Обслуживание и замена зеркал, линз, турбины (если есть).
- Общая стоимость владения (TCO) для волоконных лазеров, как правило, ниже.
Требования к обслуживанию и надежность
- Волоконные лазеры: Считаются более надежными и требуют значительно меньше обслуживания благодаря отсутствию подвижных частей в резонаторе и оптоволоконной доставке луча, не требующей юстировки.
- CO2 лазеры: Требуют регулярного обслуживания системы зеркал, проверки и пополнения газовой смеси, обслуживания вакуумной системы и турбины (в высокомощных системах). Это приводит к большим простоям и затратам на сервис.
Первоначальные инвестиции (стоимость оборудования)
Исторически станки с CO2-лазерами были дешевле. Однако с развитием технологий и увеличением объемов производства цены на станки с волоконным лазером для металла значительно снизились и продолжают снижаться, особенно для систем средней мощности. Сегодня стоимость сопоставимых по мощности систем может быть близкой, а иногда волоконные лазеры даже доступнее.
Безопасность эксплуатации
- CO2 лазеры (10.6 мкм): Излучение невидимо, но хорошо поглощается большинством органических материалов, включая кожу и роговицу глаза. Требуют защитных кабин из специальных материалов (например, поликарбоната).
- Волоконные лазеры (1.06-1.08 мкм): Излучение также невидимо, но его длина волны более опасна для сетчатки глаза, так как оно может проходить через роговицу и хрусталик и фокусироваться на сетчатке. Требуют более строгих мер безопасности, полностью закрытых кабин из материалов, не пропускающих данную длину волны, и специальных защитных очков.
Критерии выбора между CO2 и волоконным лазером
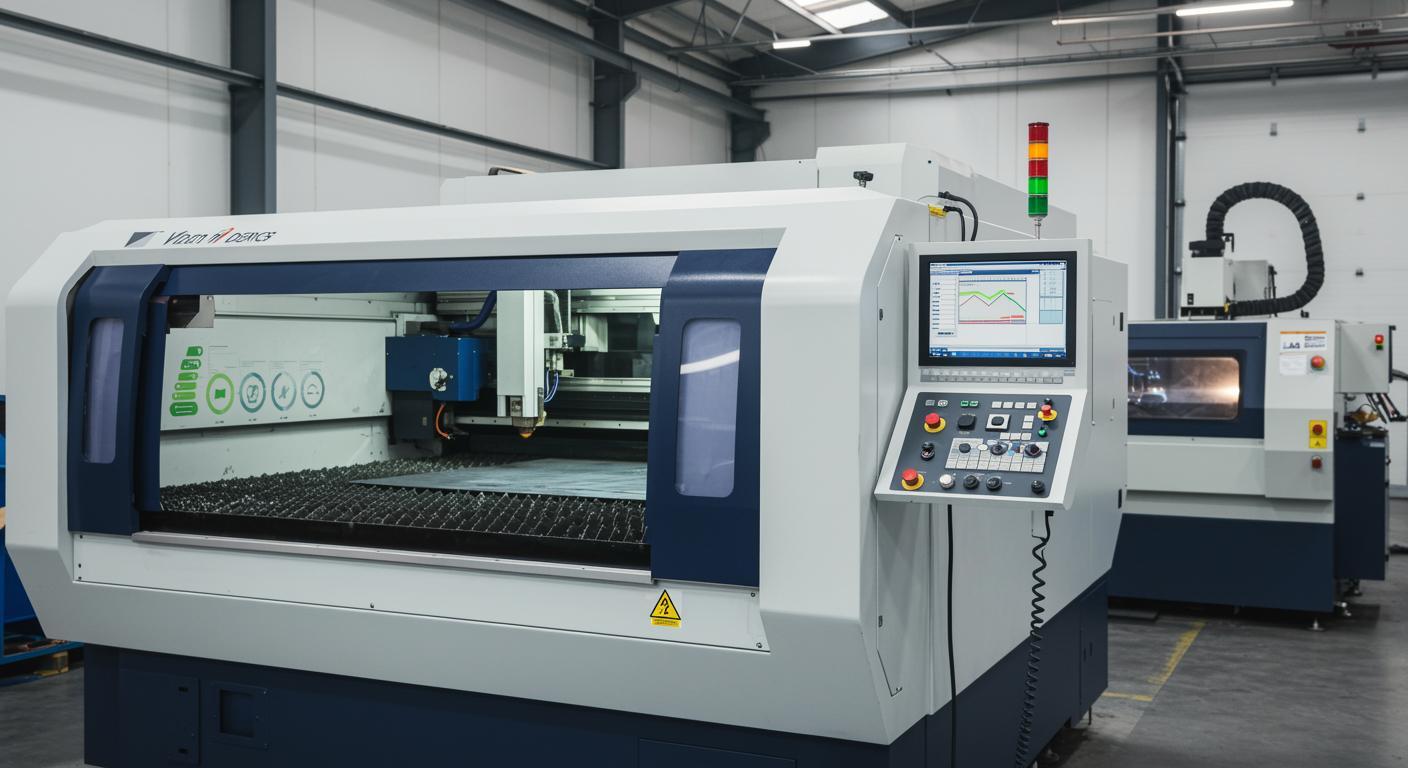
Ответ на вопрос, какой лазер лучше для резки металла, зависит от конкретных производственных задач.
Когда предпочтительнее CO2 лазер
- Универсальная резка: Если основная задача – резка широкого спектра материалов, включая металлы (преимущественно углеродистую сталь) и значительные объемы неметаллов (пластик, дерево, акрил) на одном станке.
- Специфическое качество кромки на очень толстых сталях: В некоторых редких случаях, для очень толстых углеродистых сталей (свыше 25-30 мм), где требуется определенный вид кромки, CO2-лазер с кислородной резкой может все еще давать приемлемый результат, хотя это становится все менее актуальным.
- Очень ограниченный бюджет на старое оборудование: Иногда на вторичном рынке можно найти очень дешевые CO2-станки, но их эксплуатационные расходы и надежность могут нивелировать начальную экономию.
Когда предпочтительнее волоконный (оптоволоконный) лазер
- Резка металлов как основная задача: Если 90-100% времени станок будет резать металл.
- Высокоскоростная резка тонколистового и среднелистового металла: Для стали, нержавейки, алюминия толщиной до 10-15 мм волоконный лазер обеспечит максимальную производительность.
- Резка цветных и высокоотражающих металлов: Для меди, латуни, бронзы, титана, оцинкованной стали оптоволоконный лазер резка металла является практически безальтернативным выбором.
- Низкие эксплуатационные расходы и высокая энергоэффективность: Если важна экономия на электроэнергии и обслуживании в долгосрочной перспективе.
- Минимальные требования к обслуживанию и высокая надежность: Для производств, где важны минимальные простои.
- Высокая производительность и автоматизация: Волоконные лазеры легко интегрируются в автоматизированные линии.
Анализ производственных задач как основа для выбора
Перед тем как сделать выбор лазера для резки металла, необходимо тщательно проанализировать:
- Типы обрабатываемых материалов и их процентное соотношение.
- Диапазон толщин и преобладающие толщины.
- Требования к качеству реза и скорости.
- Объемы производства (серийность).
- Бюджет на покупку и ожидаемые эксплуатационные расходы.
- Квалификация персонала и возможности обслуживания.
- Перспективы развития производства и возможные будущие задачи.
Перспективы развития CO2 и волоконных лазеров
Рынок лазерной резки металла однозначно смещается в сторону волоконных технологий.
- Волоконные лазеры: Продолжают стремительно развиваться: растут мощности (уже доступны коммерческие системы 40 кВт и выше), улучшается качество луча, оптимизируются процессы резки толстых материалов. Их доля на рынке резки металлов доминирует и будет только расти.
- CO2 лазеры: Постепенно уступают позиции в сфере резки металлов. Их развитие практически остановилось. Они, вероятно, сохранят свою нишу в универсальной резке (металлы + неметаллы) и в некоторых специфических научных или промышленных применениях, не связанных с массовой резкой металла.
Заключение
Сравнение CO2 и волоконных лазеров показывает, что для большинства задач по резке металла сегодня волоконный лазер для металла является более предпочтительным выбором благодаря своей скорости, эффективности, низким эксплуатационным расходам и способности обрабатывать широкий спектр металлов, включая цветные. Однозначного ответа на вопрос "CO2 или волоконный лазер – что лучше?" не существует без тщательного анализа конкретных производственных потребностей. Однако общая тенденция очевидна: будущее лазерной резки металла за волоконными технологиями. Тщательный выбор лазера для резки металла на основе анализа ваших задач – это ключ к повышению эффективности, снижению затрат и укреплению конкурентоспособности вашего производства.